Shrink Bags: Your Wholesale Solution for Superior Product Protection
Are you struggling to keep your products fresh, secure, and attractive during shipping and storage? YF Packaging’s Shrink Bags are here to solve your packaging woes!
Why Choose YF Packaging for Your Shrink Bags?
- Direct Manufacturer Savings: Skip the middlemen and save up to 35% on your packaging costs.
- Bulk Orders Welcome: From 5,000 to 5 million bags, we’ve got your quantity needs covered.
- Customization Experts: Get bags tailored to your exact specifications.
- Quality You Can Trust: Our rigorous testing ensures a 99.8% defect-free rate.
- Lightning-Fast Production: Receive your order in as little as 5 days for standard sizes.
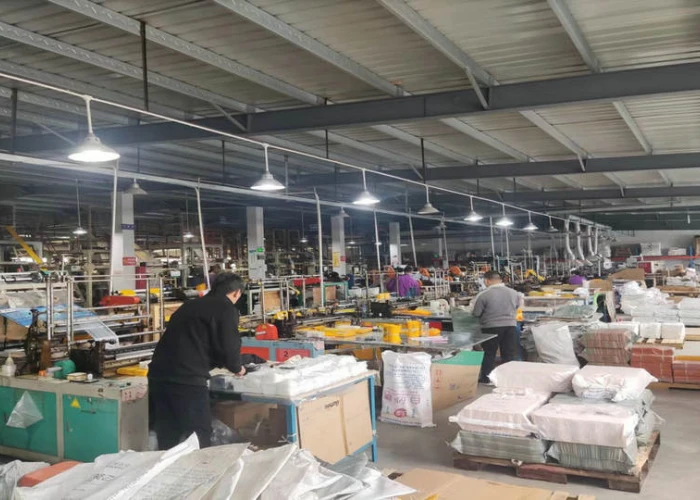
What Are Shrink Bags and Why Do You Need Them?
Shrink bags are versatile packaging solutions that conform tightly to your product when heat is applied. They’re perfect for:
- Fresh and frozen meats
- Cheeses and dairy products
- Produce and prepared foods
- Industrial parts and components
- Retail multipacks
Our shrink bags provide superior protection against moisture, oxygen, and contaminants, extending your product’s shelf life by up to 50%!
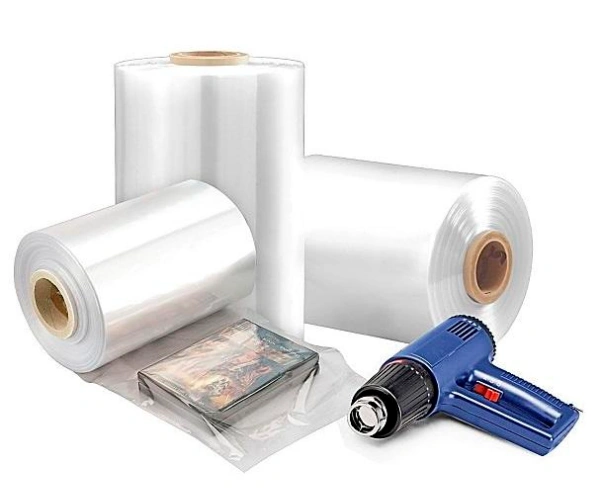
Our Shrink Bags
At YF Packaging, we offer a diverse range of high-quality shrink bags designed to meet various packaging needs across multiple industries. Here are some of our specific products:
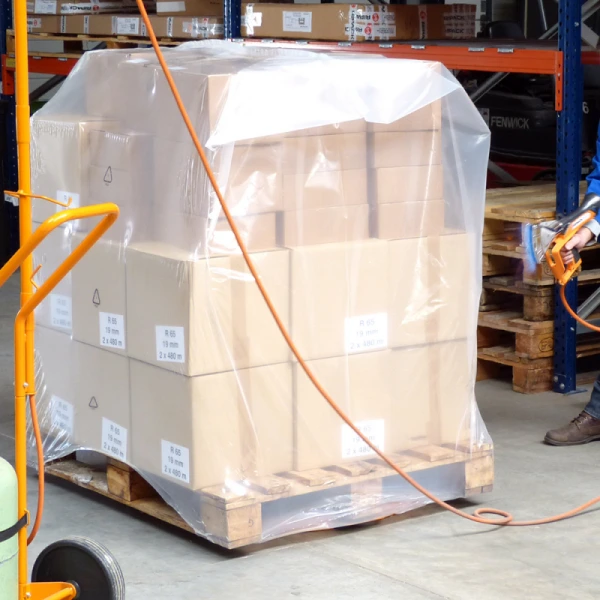
Pallet Size Shrink Bags
Our 4 Mil Pallet Shrink Bags are engineered for heavy-duty protection. These bags provide a glove-like cover for large machinery and irregular loads, ensuring they arrive in perfect condition. Key features include:
- Controlled shrink characteristics for a tight hold
- Easy application with perforated rolls
- Suitable for temporary outdoor storage and shipping
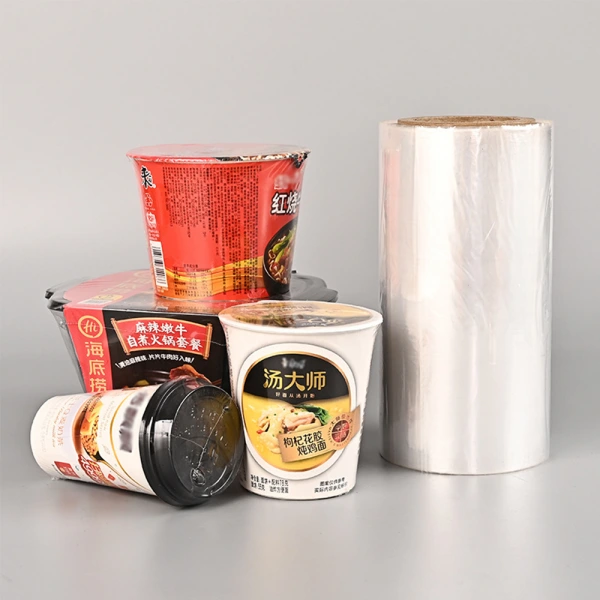
Polyethylene Shrink Bags
These polyethylene shrink bags are designed to fit snugly around products after heat application. They come in various sizes and are ideal for:
- Bundling products securely
- Protecting items during transit
- Providing a clear view of the packaged goods
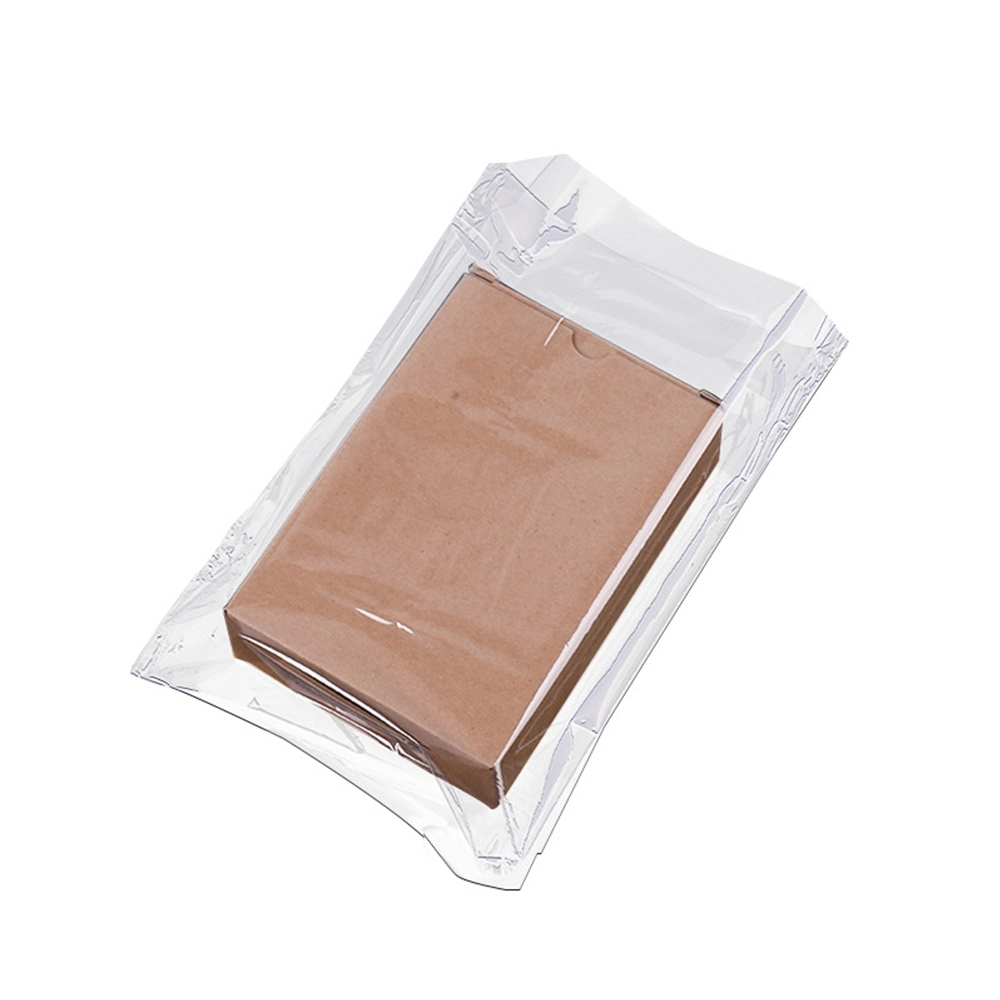
PVC Shrink Film Bags
Our PVC shrink film bags are known for their high clarity and reflective appearance. They perform well in low to high heat applications and are perfect for:
- Extending the shelf life of food products
- Preventing heat exposure issues during storage
- Offering a versatile solution for various product shapes
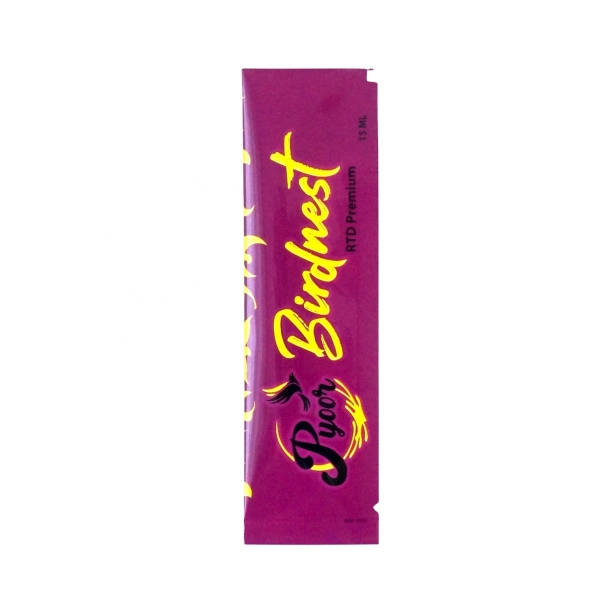
Custom Printed Shrink Bags
Enhance your brand visibility with our custom printed shrink bags. These bags can be tailored to your specifications, featuring:
- Your logo and branding displayed prominently
- Options for tamper-proof sealing
- Custom sizes and colors to fit your unique products
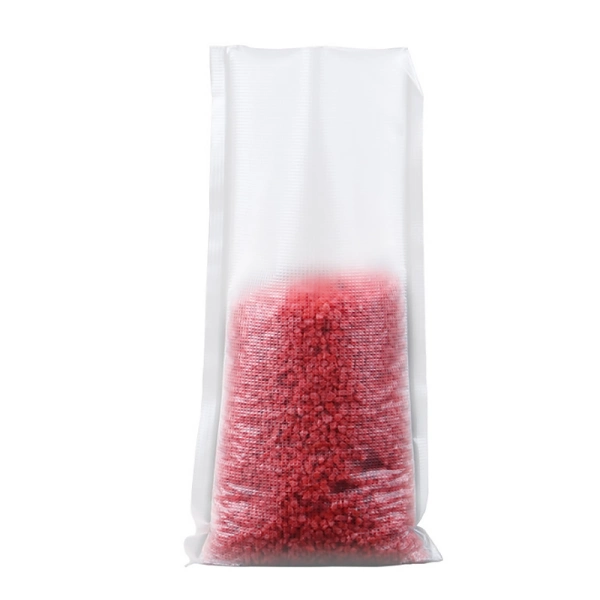
Biodegradable Shrink Bags
We are committed to sustainability with our biodegradable shrink bags that break down within 180 days in industrial compost conditions. These bags help reduce plastic waste by:
- Providing an eco-friendly alternative to standard options
- Maintaining product integrity while being environmentally responsible
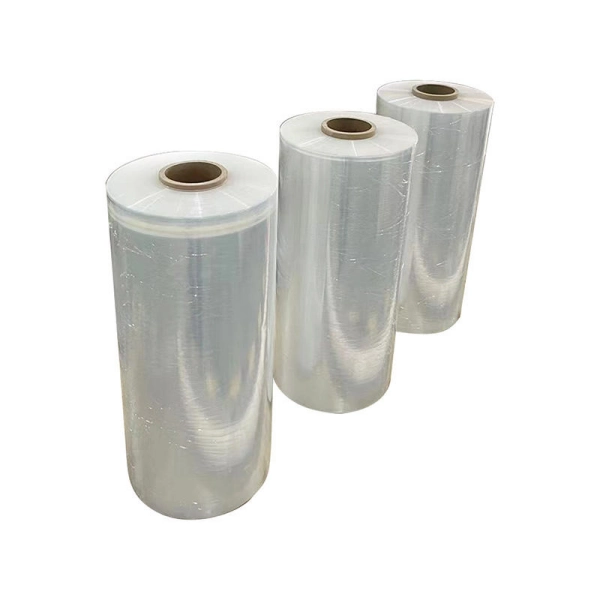
Shrink Bundling Film
Our shrink bundling film is perfect for securing multiple items together, making it ideal for:
- Retail multipacks
- Industrial parts and components
- Any application where you need to bundle products securely
Our Shrink Bag Production Process
At YF Packaging, we follow a meticulous production process to ensure our shrink bags meet the highest standards of quality and performance. Here’s a step-by-step overview of how our shrink bags are made:
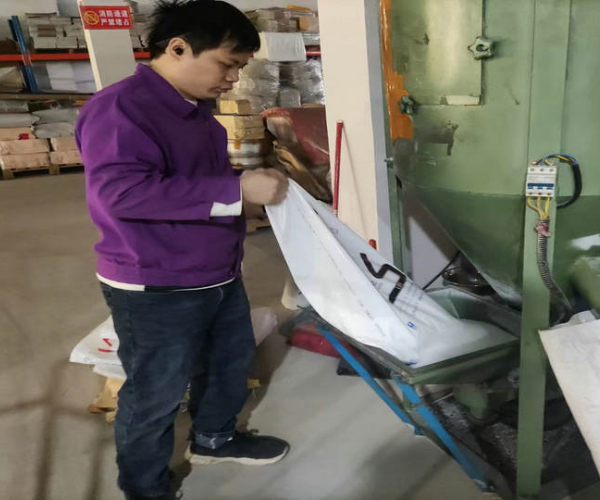
1. Material Selection
We begin by selecting high-quality raw materials, primarily polyethylene or PVC, depending on the desired properties of the shrink bags. These materials are chosen for their durability, clarity, and shrink characteristics.

2. Extrusion
The selected material is fed into an extruder, where it is melted and formed into a continuous film. This process involves:
- Heating the raw material until it reaches a molten state.
- Extruding the molten material through a die to create a flat film or tube.
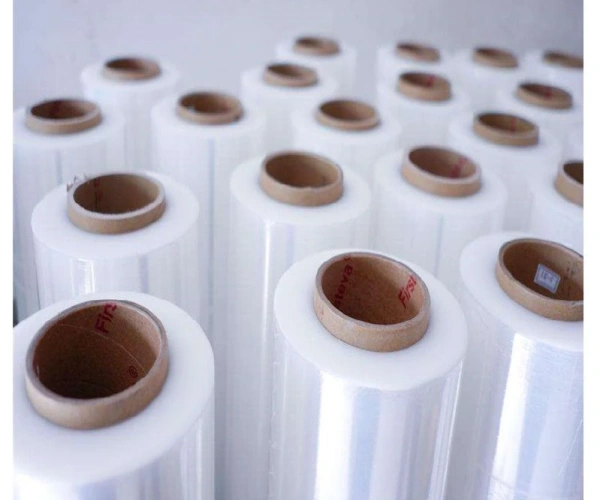
3. Cooling and Orientation
Once extruded, the film is rapidly cooled to solidify it. The cooled film undergoes orientation, where it is stretched in both machine and transverse directions. This step enhances the strength and clarity of the film, ensuring optimal performance during shrinking.
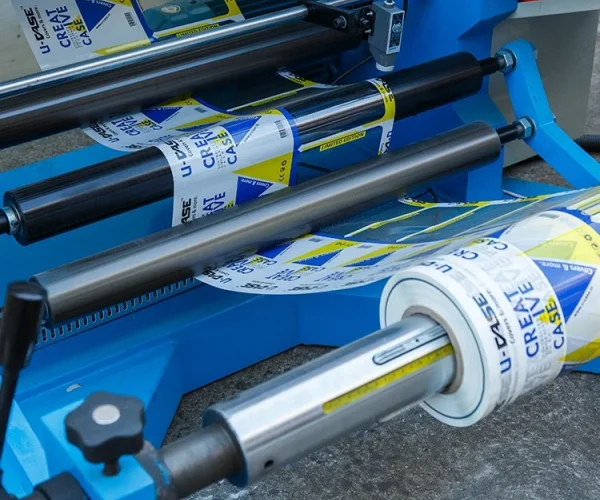
4. Heat Setting
The oriented film is then heated again to a specific temperature to “set” its molecular structure. This process locks in the orientation, allowing the film to shrink effectively when heat is applied during packaging.
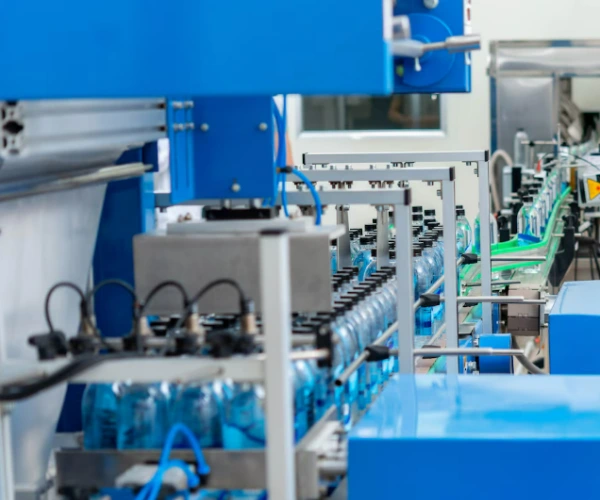
5. Slitting and Winding
After heat setting, the wide sheet of shrink film is slit into narrower rolls of desired widths. These rolls are then wound onto cores for easy handling and application.
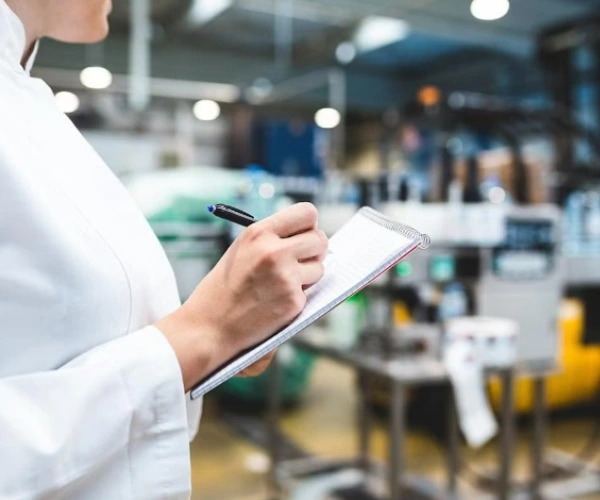
6. Quality Control
Before the shrink bags are packaged for shipment, they undergo rigorous quality control checks to ensure they meet our strict standards for thickness, clarity, and defect rates. By following these steps, we ensure that our shrink bags provide superior protection and presentation for your products while maintaining high quality and efficiency in production.
Frequently Asked Questions
Shrink bags conform tightly to your product when heat is applied, creating an attractive, secure package. Vacuum bags remove air mechanically. Our shrink bags can reduce packaging volume by up to 40% compared to vacuum bags, saving you on shipping costs.
Absolutely! Our shrink bags are designed to withstand temperatures from -40°F to 250°F (-40°C to 121°C). They’re perfect for fresh, refrigerated, and frozen applications.
It’s easy! You’ll need a heat sealer and a shrink tunnel. Don’t have the equipment? No worries! We offer affordable shrink systems that can process up to 20 products per minute, perfect for small to medium-sized operations.
Of course! Our packaging experts provide free consultations to help you seamlessly integrate shrink bags into your production line. We’ve helped over 500 businesses make the switch, increasing their packaging efficiency by an average of 40%.
Ready to Revolutionize Your Packaging?
Contact Our Sales Team Today!